Bus GNV : réception, contrôle, entretien et optimisation
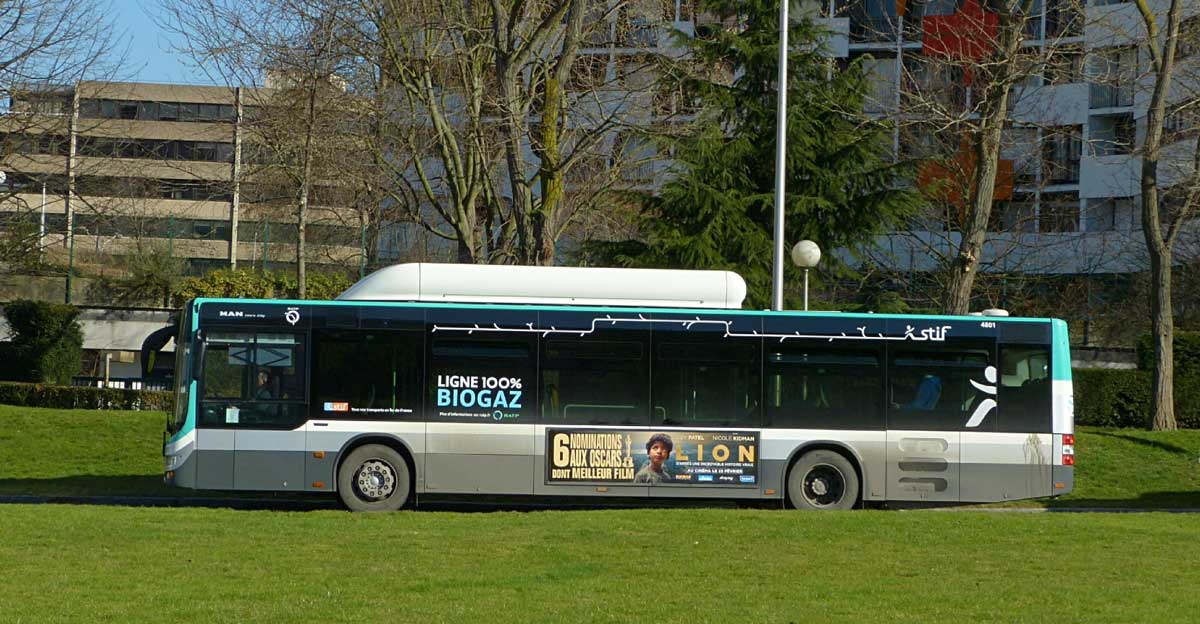
Un projet d’équipement en bus alimentés en GNV, ou un programme d’exploitation en cours depuis peu ou de nombreuses années : Gaz Mobilité propose, à travers ce dossier à destination des collectivités territoriales ou des délégataires qui exploitent un réseau de transports en commun, des éléments à connaître pour prendre livraison, contrôler et optimiser ces véhicules.
S’agissant d’un bus au GNV, outre la classique attestation de conformité qui assure que ce modèle est bien homologué pour circuler en France, la carte grise, l’attestation d’aménagement intérieur, le manuel d’utilisation du constructeur avec les préconisations d’utilisation et d’entretien, et les certificats de garantie, doit être fourni un dossier technique dédié à la chaîne d’alimentation au gaz.
Il comprend au minimum une description du circuit GNV illustrée de schémas, le plan de montage des réservoirs avec leur identification et la date d’épreuve, les instructions à suivre pour intervenir sur le circuit. S’y ajoutent les outils physiques (clés de démontage) et numériques (application de contrôle et réglage) nécessaires et spécifiques à l’utilisation et à l’entretien des véhicules reçus. Surtout pour les entités qui vont exploiter pour la première fois des bus GNV, et si ce n’est pas déjà fait, une formation à la conduite et éventuellement à la maintenance et au remplissage des réservoirs est certainement prévue par le constructeur, notamment via le concessionnaire en charge de la livraison des véhicules.
Si vous exploitez un réseau de transports en commun, vous savez sans doute que les bus sont soumis à un contrôle technique tous les 6 mois. Concernant les réservoirs et l’installation haute pression, la visite d’inspecteurs reconnus par le Cofrend (Comité français d’études des essais non-destructifs) doit être effectuée tous les 4 ans au minimum (contre 3 ans il y a quelques années).
Tout ceci pour dire qu’il est impératif de bien vérifier tout le circuit d’alimentation au GNV à réception des véhicules, ce qui passe notamment par le remplissage des réservoirs et l’observation de l’étanchéité de l’ensemble. Mais auparavant, il vous faudra contrôler sur ces contenants l’absence totale de risques de frottements et de contacts, -notamment des parties métalliques des sangles de fixation -, mais aussi de traces (impacts, brûlures, abrasions, déformations, agressions chimiques, etc.) trahissant un risque d’affaiblissement ou de perforation des parois.
Les réservoirs montés doivent être conformes aux documents remis, et les dates d’épreuve indiquées sur des supports infalsifiables et vérifiables facilement. Tout le circuit doit être exempt de possibles points d’usure par frottements, en particulier au niveau du coffrage de protection des réservoirs, et ne peut souffrir le moindre défaut de fixation. Pour info, le Cetim (Centre technique des industries mécaniques), a mis au jour que nombre des anomalies détectées sur le système d’alimentation au GNV lors des contrôles réguliers concernaient des problèmes de montage. Voilà pourquoi le l’organisme milite pour un premier contrôle obligatoire à la livraison des bus GNV.
Par qui doit être effectué le contrôle ? Par un organisme comme le Cetim, bien entendu, ou par des agents salariés des entreprises exploitantes que ces dernières font certifier par la Cofrend à la suite d’une formation dédiée. Le dernier cas est actuellement le plus répandu. Le contrôle dure en moyenne une demi-journée, un temps qui varie en fonction du véhicule et de son équipement, notamment du nombre de réservoirs à vérifier.
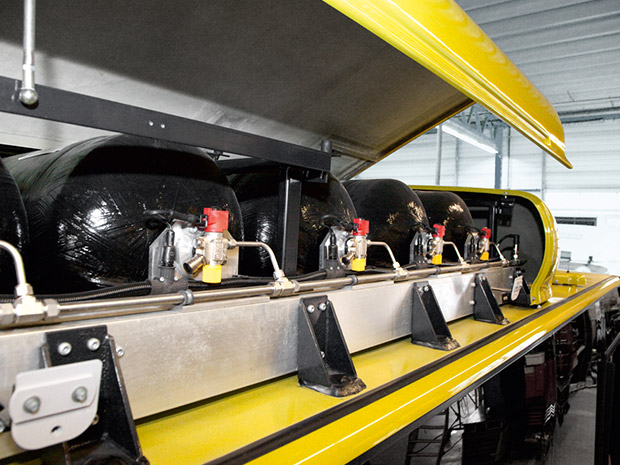
L’inspection est aussi obligatoire à la suite de certaines circonstances : si le réservoir a subi un choc ou a été soumis à une température supérieure à celle admissible déclarée par le fabricant, après une surpression majeure constatée lors du remplissage, en cas d’accident du bus, si l’installation a fait l’objet d’une modification notable ou si elle a été démontée et réimplantée sur le même ou un autre véhicule.
Des outils spécifiques sont nécessaires, parmi lesquels : luxmètre, lampe antidéflagrante, miroirs d’inspection coudés, loupe, cales d’épaisseur, produit moussant en bombe aérosol, etc. Le contrôle donne lieu à l’établissement d’un procès-verbal dont les éléments sont consignés dans la base Data-CID (Contrôle pas inspection détaillée) qui centralise depuis 15 ans tous les contrôles.
Deux niveaux d’anomalie sont actifs. Au niveau 1, il s’agit de défauts mineurs acceptables qui n’empêchent pas l’exploitation des véhicules. Le niveau 3 (le niveau 2 est prévu par la norme ISO mais n’est pas retenu ici) impose, avant contre-visite, une action : soit le remplacement et l’élimination de l’équipement concerné, soit une préconisation de remise à niveau technique.
D’origine, les bus thermiques sont rarement dotés d’une gestion intelligente des équipements et accessoires. La solution OptimACC-Cooling repose sur le remplacement d’un système non pilotable par un pilotage prédictif. Ce dernier interprète différentes données en rapport avec l’action du conducteur (accélération, décélération, braquage des roues, etc.) ou l’état (régime du moteur, vitesse, etc.) et la température de la mécanique. Sans attendre un certain seuil pour déclencher la ventilation, le dispositif permet de profiter du frein moteur, - quand l’injection est coupée -, pour faire baisser de quelques degrés le bloc, sans consommation d’énergie, et avec une vitesse moindre des ventilateurs.
Parmi les points forts de la technologie OptimACC-Cooling : l’anticipation des parcours, et la désynchronisation de la mise en route des ventilateurs avec le fonctionnement du bloc thermique. Le moteur, la boîte de vitesses et le convertisseur de couple bénéficient de durées de fonctionnement plus longues grâce à une élimination des pics de température du liquide de refroidissement.
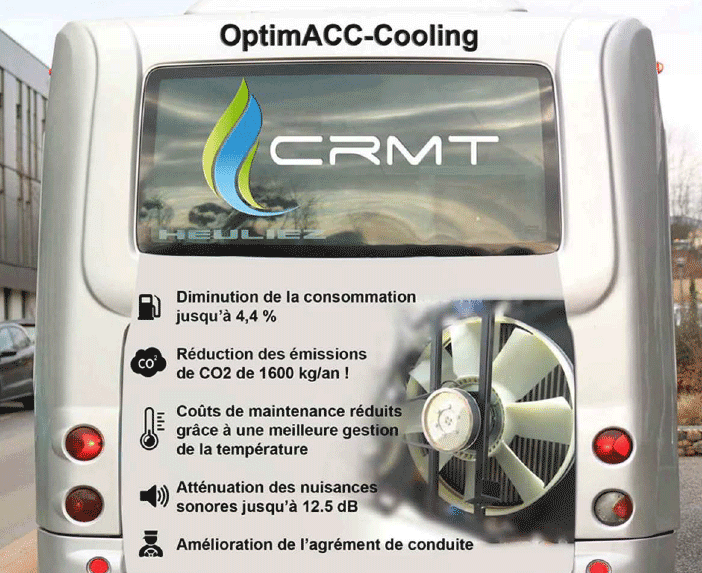
Des effets positifs obtenus grâce à une usure moins importante du système d’allumage, du catalyseur et de la sonde lambda. Sur le terrain, les bénéfices sont intéressants : élimination des ratés à l’allumage, amélioration du confort des passagers et en particulier du conducteur via un meilleur agrément de conduite, temps de réponse du moteur permettant d’insérer le véhicule plus facilement dans la circulation.
SOMMAIRE
- Réception des bus GNV
- Contrôles du système haute pression et des réservoirs GNV
- Optimisation des bus GNV : les solutions du CRMT
Réception des bus GNV
Les bus GNV commandés sont sur le point d’arriver : Que faut-il vérifier pour valider la livraison et commencer à les exploiter ? Tout d’abord, comme à la réception de tout véhicule à moteur, des documents sont remis avec les clés.S’agissant d’un bus au GNV, outre la classique attestation de conformité qui assure que ce modèle est bien homologué pour circuler en France, la carte grise, l’attestation d’aménagement intérieur, le manuel d’utilisation du constructeur avec les préconisations d’utilisation et d’entretien, et les certificats de garantie, doit être fourni un dossier technique dédié à la chaîne d’alimentation au gaz.
Il comprend au minimum une description du circuit GNV illustrée de schémas, le plan de montage des réservoirs avec leur identification et la date d’épreuve, les instructions à suivre pour intervenir sur le circuit. S’y ajoutent les outils physiques (clés de démontage) et numériques (application de contrôle et réglage) nécessaires et spécifiques à l’utilisation et à l’entretien des véhicules reçus. Surtout pour les entités qui vont exploiter pour la première fois des bus GNV, et si ce n’est pas déjà fait, une formation à la conduite et éventuellement à la maintenance et au remplissage des réservoirs est certainement prévue par le constructeur, notamment via le concessionnaire en charge de la livraison des véhicules.
Des contrôles à effectuer
Un cahier des charges a sans doute été établi avant le passage de la commande des bus GNV. Un premier contrôle à effectuer est que les véhicules et leurs équipements correspondent en tous points aux exigences formulées dans le document.Si vous exploitez un réseau de transports en commun, vous savez sans doute que les bus sont soumis à un contrôle technique tous les 6 mois. Concernant les réservoirs et l’installation haute pression, la visite d’inspecteurs reconnus par le Cofrend (Comité français d’études des essais non-destructifs) doit être effectuée tous les 4 ans au minimum (contre 3 ans il y a quelques années).
Tout ceci pour dire qu’il est impératif de bien vérifier tout le circuit d’alimentation au GNV à réception des véhicules, ce qui passe notamment par le remplissage des réservoirs et l’observation de l’étanchéité de l’ensemble. Mais auparavant, il vous faudra contrôler sur ces contenants l’absence totale de risques de frottements et de contacts, -notamment des parties métalliques des sangles de fixation -, mais aussi de traces (impacts, brûlures, abrasions, déformations, agressions chimiques, etc.) trahissant un risque d’affaiblissement ou de perforation des parois.
Les réservoirs montés doivent être conformes aux documents remis, et les dates d’épreuve indiquées sur des supports infalsifiables et vérifiables facilement. Tout le circuit doit être exempt de possibles points d’usure par frottements, en particulier au niveau du coffrage de protection des réservoirs, et ne peut souffrir le moindre défaut de fixation. Pour info, le Cetim (Centre technique des industries mécaniques), a mis au jour que nombre des anomalies détectées sur le système d’alimentation au GNV lors des contrôles réguliers concernaient des problèmes de montage. Voilà pourquoi le l’organisme milite pour un premier contrôle obligatoire à la livraison des bus GNV.
Contrôles du système haute pression et des réservoirs GNV
Réservoirs, embout de remplissage, détendeur, témoin de pression ou jauge, vannes, régulateur et limiteur de débit, tuyauteries rigides et flexibles, etc. : c’est tout le circuit haute pression qui est vérifié périodiquement selon une procédure en 9 étapes :- Identification des réservoirs par leur marquage ;
- Inspection de l’environnement proche du réservoir ;
- Inspection du système de fixation et de maintien du réservoir ;
- Contrôle d’étanchéité ; Inspection générale du circuit haute pression ;
- Inspection des dispositifs de surpression ; inspection des électrovannes ;
- Recherche d’endommagements sur les réservoirs ;
- Inspection de l’embout de remplissage
Par qui doit être effectué le contrôle ? Par un organisme comme le Cetim, bien entendu, ou par des agents salariés des entreprises exploitantes que ces dernières font certifier par la Cofrend à la suite d’une formation dédiée. Le dernier cas est actuellement le plus répandu. Le contrôle dure en moyenne une demi-journée, un temps qui varie en fonction du véhicule et de son équipement, notamment du nombre de réservoirs à vérifier.
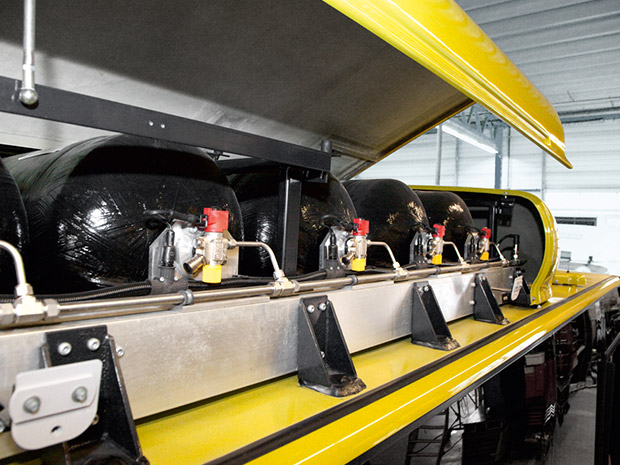
Périodicité
L’installation haute pression des bus alimentés au GNV doit impérativement être contrôlée tous les 4 ans à partir de la date de première mise en circulation. Et ce, que les véhicules circulent ou soient immobilisés. Même lorsque les engins ne quittent pas le dépôt, leurs circuits GNV continuent à vieillir.L’inspection est aussi obligatoire à la suite de certaines circonstances : si le réservoir a subi un choc ou a été soumis à une température supérieure à celle admissible déclarée par le fabricant, après une surpression majeure constatée lors du remplissage, en cas d’accident du bus, si l’installation a fait l’objet d’une modification notable ou si elle a été démontée et réimplantée sur le même ou un autre véhicule.
Des outils spécifiques sont nécessaires, parmi lesquels : luxmètre, lampe antidéflagrante, miroirs d’inspection coudés, loupe, cales d’épaisseur, produit moussant en bombe aérosol, etc. Le contrôle donne lieu à l’établissement d’un procès-verbal dont les éléments sont consignés dans la base Data-CID (Contrôle pas inspection détaillée) qui centralise depuis 15 ans tous les contrôles.
Deux niveaux d’anomalie sont actifs. Au niveau 1, il s’agit de défauts mineurs acceptables qui n’empêchent pas l’exploitation des véhicules. Le niveau 3 (le niveau 2 est prévu par la norme ISO mais n’est pas retenu ici) impose, avant contre-visite, une action : soit le remplacement et l’élimination de l’équipement concerné, soit une préconisation de remise à niveau technique.
Optimisation des bus GNV : les solutions du CRMT
Le CRMT propose différentes solutions pour optimiser le fonctionnement des bus diesel, hybrides et alimentés au gaz. Elles sont pour la plupart regroupées sous l’appellation générique OptimACC (Optimisation des accessoires), et se déclinent en OptimACC-Cooling, OptimACC-Air, OptimACC-Elec, pour la gestion intelligente, respectivement, du refroidissement moteur, du compresseur d’air et de l’alternateur, à intégrer ensemble ou séparément, en rétrofit ou première monte.OptimACC-Cooling en exemple
L’offre OptimACC-Cooling, exploitée par exemple par la Semitan à Nantes (44) afin d’améliorer l’usage des Mercedes Citaro, vise, entre autres, à économiser l’énergie (jusqu’à 4,4% en moins), réduire les émissions de CO2 (de l’ordre de 1.600 kg par an et par bus) et le bruit (-12,5 dB déjà obtenus), procurer un meilleur agrément de conduite pour les chauffeurs, et à faciliter les opérations de maintenance des véhicules.D’origine, les bus thermiques sont rarement dotés d’une gestion intelligente des équipements et accessoires. La solution OptimACC-Cooling repose sur le remplacement d’un système non pilotable par un pilotage prédictif. Ce dernier interprète différentes données en rapport avec l’action du conducteur (accélération, décélération, braquage des roues, etc.) ou l’état (régime du moteur, vitesse, etc.) et la température de la mécanique. Sans attendre un certain seuil pour déclencher la ventilation, le dispositif permet de profiter du frein moteur, - quand l’injection est coupée -, pour faire baisser de quelques degrés le bloc, sans consommation d’énergie, et avec une vitesse moindre des ventilateurs.
Parmi les points forts de la technologie OptimACC-Cooling : l’anticipation des parcours, et la désynchronisation de la mise en route des ventilateurs avec le fonctionnement du bloc thermique. Le moteur, la boîte de vitesses et le convertisseur de couple bénéficient de durées de fonctionnement plus longues grâce à une élimination des pics de température du liquide de refroidissement.
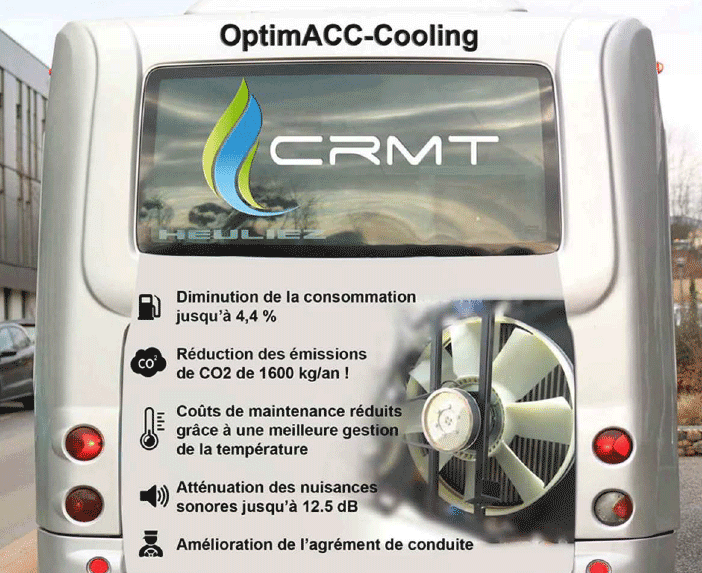
Détendeur évolution
Un problème sur un bus GNV ? CRMT va chercher à le gommer. Ainsi pour les modèles Heuliez et Iveco équipés du moteur Cursor 8 CNG, l’entreprise propose, en rétrofit, une solution pour un fonctionnement moteur régulier et performant. Globalement, le système, - composé d’un circuit de réchauffement du GNV, d’un détendeur, d’un filtre, d’une électrovanne et d’une vanne thermostatique -, permet un meilleur contrôle de la régulation de gaz et la réduction de la fréquence de maintenance.Des effets positifs obtenus grâce à une usure moins importante du système d’allumage, du catalyseur et de la sonde lambda. Sur le terrain, les bénéfices sont intéressants : élimination des ratés à l’allumage, amélioration du confort des passagers et en particulier du conducteur via un meilleur agrément de conduite, temps de réponse du moteur permettant d’insérer le véhicule plus facilement dans la circulation.
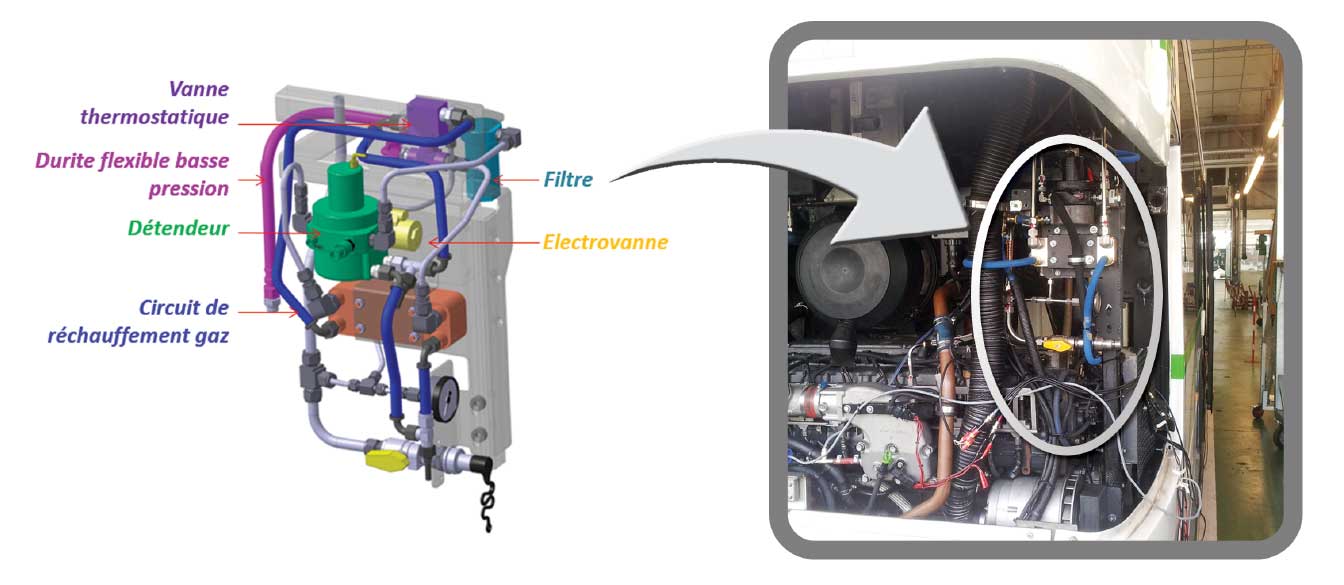
Un média soutenu par ses partenaires
Si Gaz-Mobilite.fr vous informe gratuitement et sans publicité sur toute l'actualité de la filière GNV, c'est grâce au soutien d'une quarantaine de partenaires.
Si Gaz-Mobilite.fr vous informe gratuitement et sans publicité sur toute l'actualité de la filière GNV, c'est grâce au soutien d'une quarantaine de partenaires.
Vous souhaitez nous soutenir ?
Rejoignez nos partenaires !
Rejoignez nos partenaires !